Better results. Less chemistry.™
- Surface Cleaning Chemistry
- Metal Finishing Chemistry
- Wastewater Treatment Chemistry
- Specialty Applications
Hubbard-Hall OnDemand
24-7 access for current customers. Easy ordering, document download, and shipment history.
Hubbard-Hall Store
A select group of Hubbard-Hall products is also available for purchase through our e-commerce store.
Wastewater Treatment Chemistry
Specialty Applications
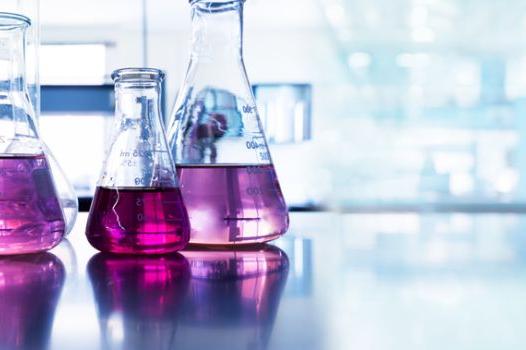
State-of-the-Art Technology
Our tech-enhanced cleaning transforms your process, boosts efficiency, and promotes environmental sustainability.
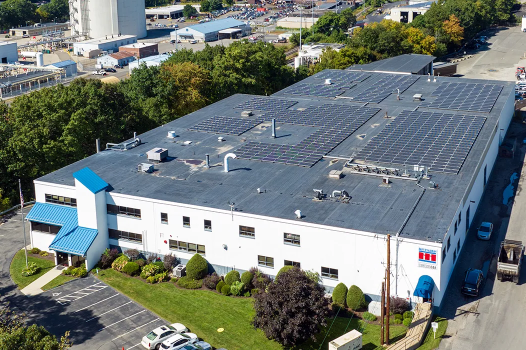
About Hubbard-Hall
Our mission is to help manufacturers tackle complex surface cleaning, finishing, and wastewater treatment problems.
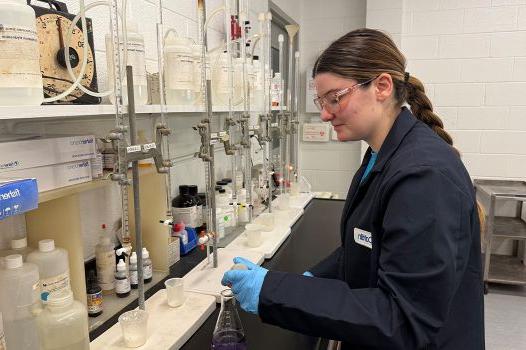
Proven Results
With over six generations of expertise, our team thrives on solving challenges. Your success is our success.
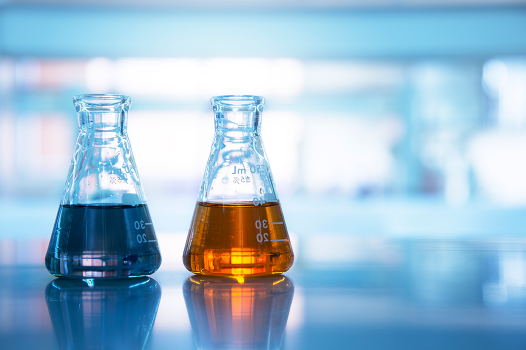
Resource Library
Access product bulletins, safety information, and product documents, along with more resources for additional information.
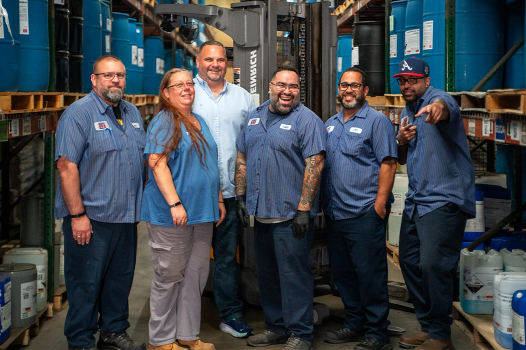
Contact Our Experts
Our people. Your problem solvers. Connect with a Hubbard-Hall representative today.
Hubbard-Hall OnDemand
24-7 access for current customers. Easy ordering, document download, and shipment history.
Hubbard-Hall Store
A select group of Hubbard-Hall products is also available for purchase through our e-commerce store.
Enhancing Aluminum Treatment: Optimizing Bath Life for Quality Assurance
Blog

In the process of aluminum cleaning, managing zincate drag-in and avoiding blistering issues is important for ensuring quality. A customer case study reveals a solution that balances quality maintenance and cost-effectiveness, highlighting the importance of improving treatment processes.
When a manufacturing customer consistently faced blistering concerns around the third metal turnover (MTO). Their innovative response was to draw a line: “We refresh our bath every two MTOs,” a decision they transformed into a customer-focused marketing strategy, emphasizing their commitment to superior quality over competitors.
However, financial realities eventually prompted a reassessment. Upon analysis by our team of experts, we found the cause of the blisters was an excessive use of zincate.
They adopted a modified “double zincate” technique, adjusting the duration of the zincate process to reduce drag-in. Initially overusing zincate during the second treatment, resulting in a visually dark coating, they refined the process by shortening the duration. This sacrifice in appearance extended their bath life significantly.
Six months later, equipped with the achieved zincate technique, they demonstrated to customers their three MTO dumping strategies, balancing quality assurance and operational efficiency. This approach maintained quality standards while underscoring their commitment to excellence.
This example demonstrates the importance of optimizing your processes. By modifying the zincate process, this company not only extended bath life but also highlighted its dedication to quality, maintaining its competitive edge.
To learn more, listen to the full podcast here!